hard anodizing aluminum diy
Ad Anodized round and square Extrusions and many more stocked shapes. This is called hard coat or hard anodizing.
Fizz the aluminium in caustic soda solution until it looks a nice grey colour.
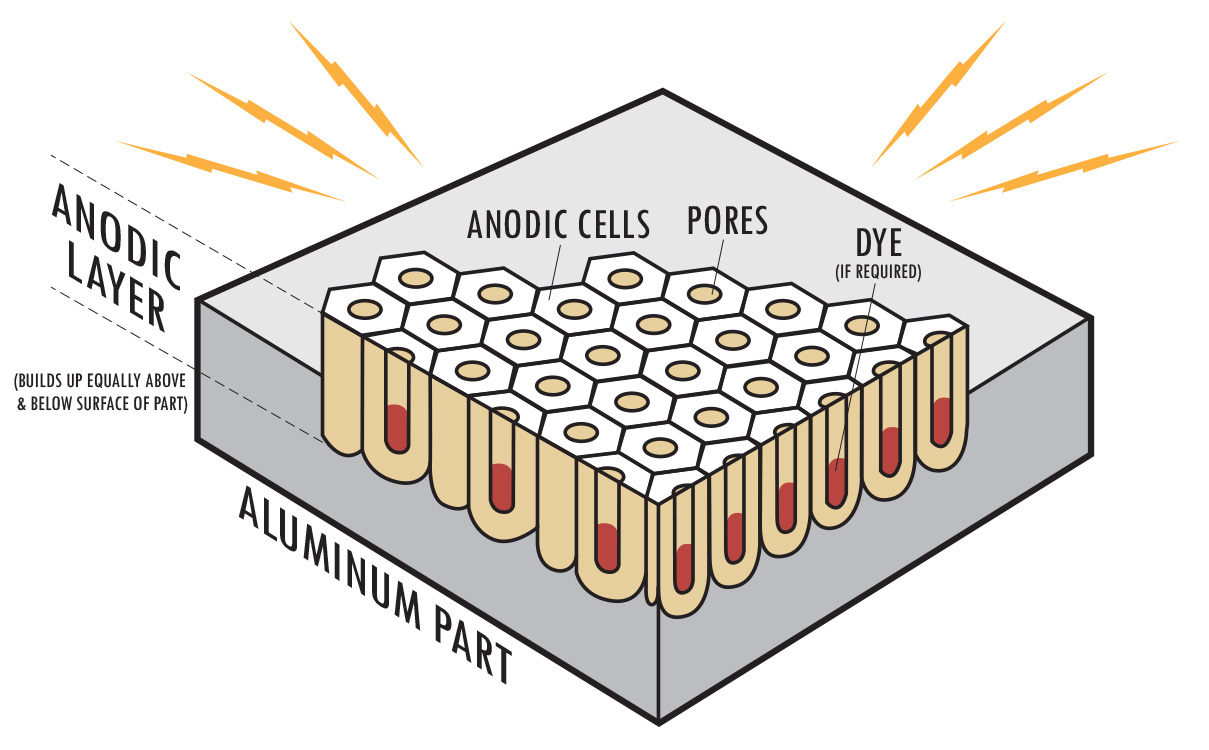
. That is the type of anodizing that takes dye well and is typically used mainly for cosmetic purposes but also adds a hard aluminum oxide coating to the part that is very corrosion resistant as well as wear resistant and has electrical insulating properties. Rinse a second time in the distilled water and dunk the parts in the dye. This results in a slightly thicker surface layer on the aluminum part.
It is possible to achieve a 002 thickness with a 50 Penetration and 50 Buildup on the surface. Step by Step home DIY anodizing of aluminium. This will be for type II anodizing type 2 anodizing.
Related
Dip first in the distilled water for 10-15 seconds then rinse in the acid neutralizer tank for 5 minutes. Turn off the power and remove your parts from the anodizing tank. For type III hard anodizing the temperature must be only 2-4C.
Before beginning the process one should calculate the liters or gallons of solution needed while taking into account the recommended ratio of acid in the anodizing bath 15 to 18. For that purpose the aluminum piece is dipped into a sodium hydroxide solution for a short time. Normally for Type II anodising we have our acid bath around 15-20 degrees.
This layer is extremely hard and can significantly increase the wear and corrosion resistance of aluminum. The temperature often rises during the anodising process. The anodizing solution that is most often used for anodizing aluminum is sulfuric acid.
The exact steps any home DIY anodizer is going to take are dictated by time available resources attention to detail and various other factors. Cases panels a CNC router parts for machines and have been wanting to improve the quality of my buil. Hard anodising is performed with a weaker solution of sulfuric acid and a lower temperature acid bath.
The anodizing voltage is also increased to 50-90 volts depending on the type of aluminum being used this is a very hard and highly wear-resistant coating. Did you make this project. It is a much thicker and harder coating than a standard anodize coating and is not usually dyed.
After rinsing the aluminum piece with deionized water the final cleaning needs to be done with acetone. I have been making all types of things from aluminum. Type II Sulfuric acid anodize has a thickness of 00002 to.
Hard anodising is performed with a weaker solution of sulfuric acid and a lower temperature acid bath. Im getting ahead of myself though. Hard anodizing requires higher voltageamperage and a chiller to keep the solution at around 32 F.
As the thickness increases the required power to biuld up the thickness increases as well. The temperature often rises during the anodising process. This will give a nice even surface finish that will look good after anodizing.
You also need a big power rectifier as well. The anodic film itself grows at the aluminium aluminium oxide. Aluminium Anodization at Home Step 1.
Type II anodizing process uses sulfuric acid instead of chromic acid. In the case of aluminium the anodising process forms a layer of aluminium oxide - Al203 - or corundum which is very hard relatively inert electrically insulating and can absorb dyes to colour the film. Aluminum alloys are highly variable so.
3 Run a DC voltage through it. Anodizing parts in my garageI am an amazon affiliate and make profits from the links belowRed dyehttpsamznto2JoKYnhBlue dyehttpsamznto2Hvtsw5Hot. The Theory 1 Clean it 2 Put it in an acidic electrolyte.
Get your respirator within hands reach. But I would think that for your conditions this process would protect as well unless the conditions are really brutal. Before anodizing however we need to remove the natural aluminum oxide layer from the metal surface.
If playback doesnt begin shortly try restarting your device. The lower the temperature the harder the anodic coating. How to Anodize Aluminum the DIY Way Scotch-Brite the Aluminum.
Hardcoat Type III Anodizing System Hardcoat Type III aluminum anodizing is a coating frequently found on firearms and aircraft parts. Type III anodizing usually needs a large chiller to lower the anodizing temperature to aero degree C. Hard anodizing results in a darker finish and can only be dyed with dark color.
Type II Sulfuric Acid Anodize. The DIY anodizing of aluminium is as simple as mixing 10 to 20 Sulphuric Acid solution with distilled water. Hard anodising is performed with a weaker solution of sulfuric acid and a lower temperature acid bath.
Vinegar leaves dark traces on edges that voltage doesnt reach try to align center and use multiple. Standard dyed Type II anodize is generally around 075 - 10 mil thousands of an inch thickness. Here is my quick guide to home aluminium anodizing - but dont blame me if it doesnt work.
Prepare one tank of distilled water and another with your acid neutralizer. Put on your safety glasses. Mix up 10 to 20 Sulphuric Acid.
Angle bar channel tube F H h and T sections. What to see the the start of the home aluminium anodising guide.
Homemade Anodizing Automatic Artisan
How To Anodize Aluminum At Home Make It From Metal
Anodising Aluminium At Home Results
Diy Anodize Aluminum At Home With A Battery Charger Youtube
Category Anodizing Aluminum Observations
Diy Manual Mechanic Anodize The Aluminum Diy Coloring
Shopbuilt How To Anodize Aluminum Youtube
Category Anodizing Aluminum Observations
Diy How To Anodize Aluminum At Home Youtube
Anodizing Aluminium At Home First Experiments
Mini Slingshot How To Anodize Aluminum Diy Giaco Giaco Youtube
Anodising Aluminium At Home Results
Everything You Need To Know About Anodizing Aluminum 3erp
How To Anodize Aluminum The Federal Group Usa
How To Anodize Aluminum My Approach On Diy Small Scale Anodizing By Deeworks Youtube
Diy Aluminium Anodising How To Improve Your Anodising
Anodising Aluminium At Home Results
Everything You Need To Know About Anodizing Aluminum 3erp
How To Anodize Aluminum Parts Easily In The Home Shop Msfn Youtube